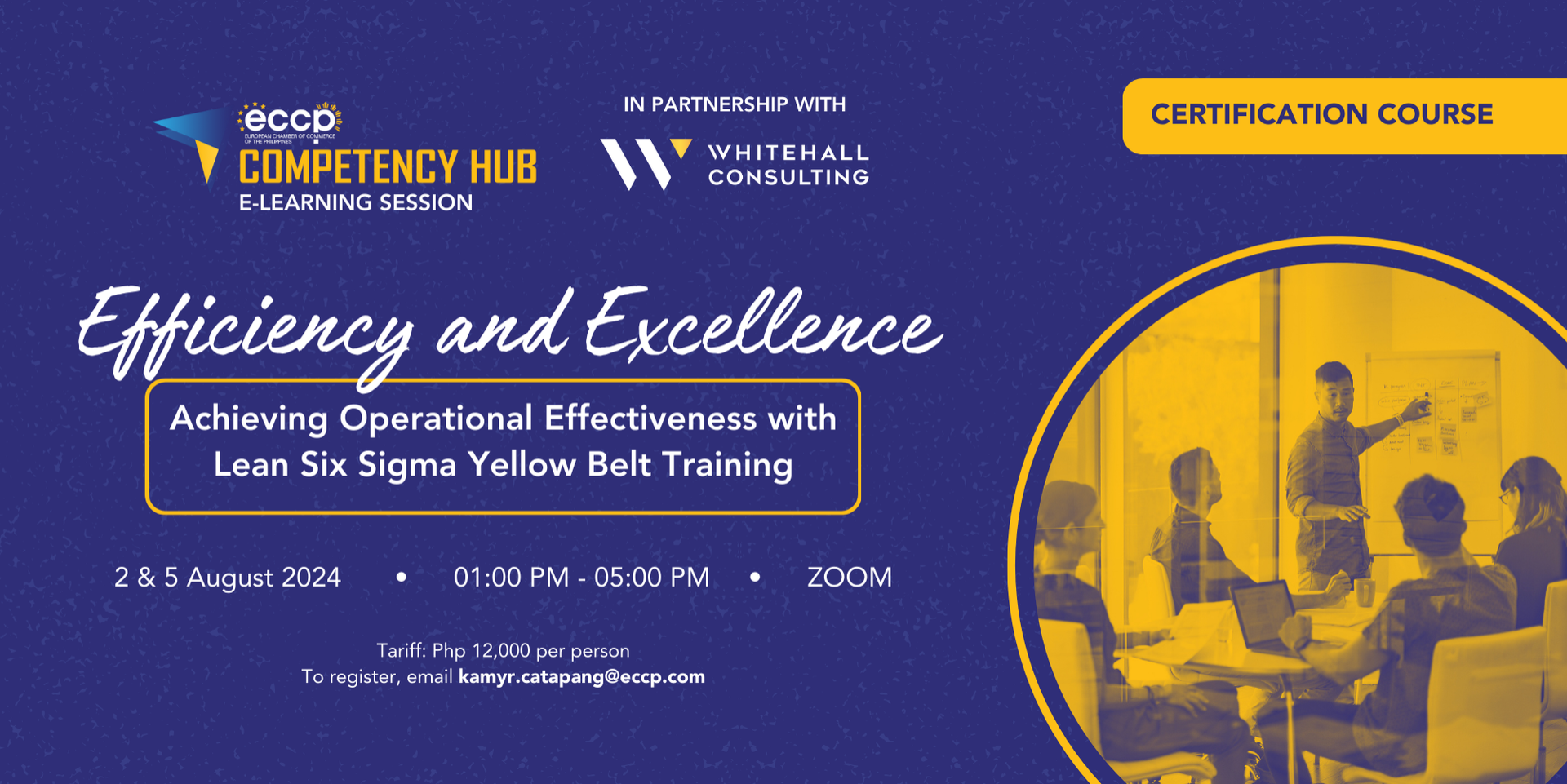
Efficiency and Excellence: Achieving Operational Effectiveness with Lean Six Sigma Yellow Belt Training
In an increasingly competitive business environment, achieving operational excellence and efficiency is key. This Lean Six Sigma Yellow Belt Training aims to equip professionals with the knowledge and skills to use Lean Six Sigma methodologies to improve business processes. This training emphasizes hands-on exercises, interactive case studies, and real-world applications to solidify understanding.
Participants will learn to streamline operations, reduce waste, improve quality, and enhance customer satisfaction using the proven Lean Six Sigma approach. Gain a solid understanding of the DMAIC (Define, Measure, Analyze, Improve, Control) process, a systematic, scientific approach to process improvement.
Learning Objectives:
By the end of the training event, participants will be able to:
- Understand the principles and values of Lean Six Sigma
- Apply Lean Six Sigma methodologies to improve business processes
- Use DMAIC for structured problem-solving and process improvement
- Employ various Lean Six Sigma tools for data collection and analysis
- Promote a culture of continuous improvement and operational efficiency
Training Outline:
I. Introduction to Lean Six Sigma
- Understand the origins and principles of Lean and Six Sigma
- Describe the importance of Lean Six Sigma as an organizational strategy
- Identify the different roles and responsibilities
- Describe the different phases of the DMAIC process improvement model
II. Define Phase - Set-up the right projects right
- Project Charter: Developing a clear project scope, goals, and stakeholders.
- VOC to CTQ: Translating Voice of Customer (VOC) into Critical to Quality (CTQ) elements—defining what's essential from a customer's perspective.
- SIPOC: Creating a high-level process map (Suppliers, Inputs, Process, Outputs, Customers) to provide an overview of the project.
III. Measure Phase - Quantify the current performance
- Baseline Data Collection: Collecting relevant data to understand current performance.
- Basic Statistics: Using basic statistical tools to summarize data.
- Data Visualization: Presenting data visually using tools such as trend charts, Pareto charts, histograms, and box plots
IV. Analyze - Validate the sources of wastes and variations
- Swimlane: Using swimlane diagrams to visualize the flow of processes.
- 8 Wastes: Identifying the eight types of wastes in a process and working to reduce or eliminate them.
- Quick Wins & Lean Fixes: Identifying and implementing quick, effective solutions for immediate improvements.
- Cause & Effect Analysis: Using the Fishbone Diagram (Ishikawa Diagram) to identify root causes of problems.
V. Improve - Achieve breakthrough performance level
- Prioritization Matrix: Prioritizing potential improvements based on their impact and effort.
- Implementation Plan: Creating a detailed action plan with a Gantt chart to guide improvement efforts.
- Before & After Analysis: Comparing process performance before and after the implementation of improvements
VI. Control -Sustain the gains
- Standardization: Establishing standard operating procedures to ensure the consistency of the improved process.
- Response and Monitoring Plan: Setting up mechanisms to monitor the improved process and respond to any deviations.
- Benefits Realization: Tracking the benefits obtained from the implemented improvements to assess the success of the project
Delivery Method: The training will be delivered using the following:
- Interactive Lectures: To present theories, principles, and practices related to Lean Six Sigma.
- Hands-on Exercises: To provide practical experience in applying Lean Six Sigma tools.
- Group Discussions: To promote exchange of ideas and experiences.
- Case Studies: To demonstrate practical applications of Lean Six Sigma in realworld contexts.
Note: The training program can be customized based on the specific needs and objectives of the organization or participants.
Additional Resources: To complement the training program, participants will receive a comprehensive training manual, reference materials, and access to online resources for further learning.
Certification: Participants who successfully complete the training will be awarded a certificate of completion.